Every product has a useful life and a life expectancy, and bridges are no different. The typical design life for a bridge is between 75 and 100 years. Over time, deterioration is inevitable and routine maintenance must be performed in order to reach the full design life. Since bridge decks see the most wear of any component of the bridge and are exposed to deicing salts in the Northeast, it is typical that they may need a complete replacement. Most of the decks being replaced today are over 35-years-old and have plain reinforcing from the original construction. Current deck replacements allow for the evaluation and potential use of alternate reinforcing materials that may not have been in regular use during the original construction. As testing and materials advance and are more available, our engineering toolbox grows as well.
Using Black Bar to Reinforce the Concrete
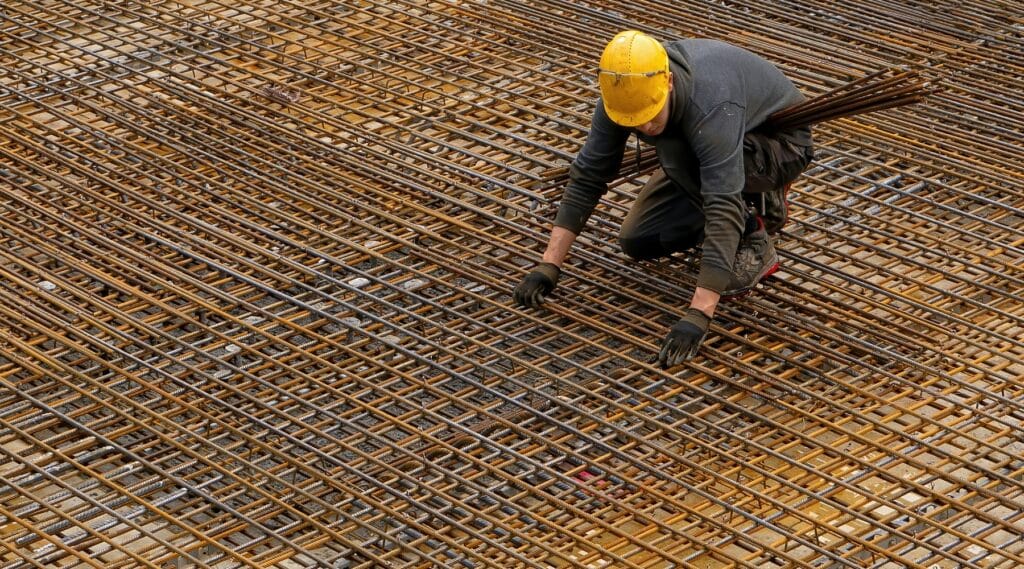
Almost all bridge decks are made of reinforced concrete. Concrete is designed as a strong compressive and durable material, with limited capacity to carry tension without cracking. For this reason, reinforcing is cast into the concrete to carry the tension loads. Traditional reinforced concrete uses a carbon-steel reinforcing commonly referred to as black bars. Black bar has been used dating back to 1911 when the grade was 33 ksi. Today, ASTM A615 grade 60 ksi is most commonly used, with strengths up to 100 ksi. Bars have also evolved from square/smooth shapes to round and deformed to facilitate bonding with the concrete.
Black, plain reinforcing is uncoated plain steel. When it is exposed to moisture and the chloride penetration from the deicing salts, the steel begins to oxidize, which causes the steel to rust and expand. Since the reinforcing is cast into the concrete, when it tries to expand, there is nowhere for it to expand to. This results in the concrete cracking to relieve the pressure of the expansion, which in turn allows for more voids and moisture to penetrate the rebar which accelerates the deterioration of the steel bar, and ultimately the capacity of the structural member.
The Epoxy Evolution
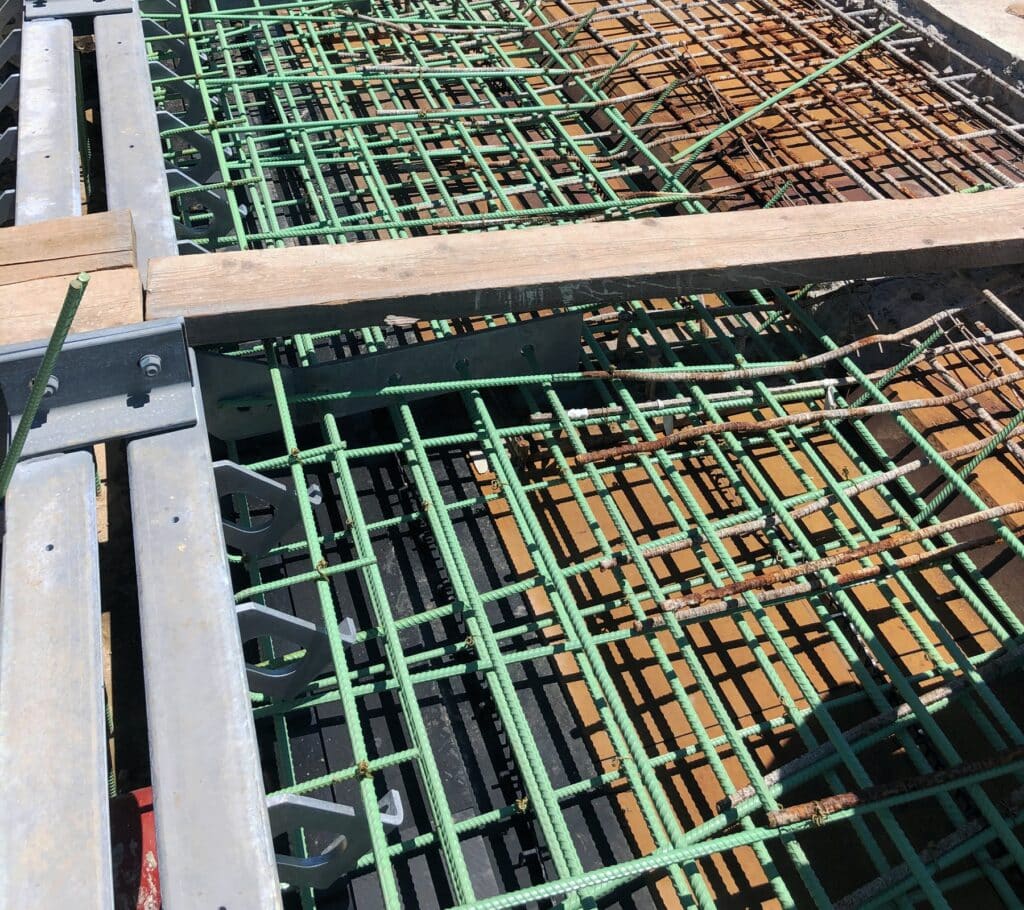
Starting in 1973, an epoxy coating has been used in an attempt to protect the steel reinforcing from corroding and to extend the life of bridge decks and other structures exposed to harsh elements. Typical epoxy coated rebar encases the steel bars in a green epoxy in a certified plant which increases the corrosion resistance of the bars. However, this coating is susceptible to damage during shipping and placement and often has to be touched up with a hand applied repair coating in the field. When these touch ups or defects in the coating are missed, the bar reacts like an uncoated bar and may not provide the intended protection.
Recent Options for Corrosion Resistance
In recent years, the manufacturing and use of stainless steel, chromium, and Glass Fiber Reinforced Polymer (GFRP) reinforcing bars have become more common and readily available. Stainless steel and chromium provide a product in which the composition of the chromium content allows the bar itself to be more resistant to corrosion. GFRP bars are typically used in straight-bar applications, since the bent bars need to be formed and are still considered cost prohibitive. These bars are formed with bundled fibers embedded in a resin that allows it to carry tensile loads. The bars are lightweight and easy to handle. The GFRP bars are typically used in conjunction with other types of steel reinforcing which is used for the bent bar applications. These applications illustrate just one alternative that is considered when investing the rehabilitation of bridge decks, allowing for the consideration of anticipated life and expected use of the structure and potentially allowing the rehabilitated deck to last even longer than the first.
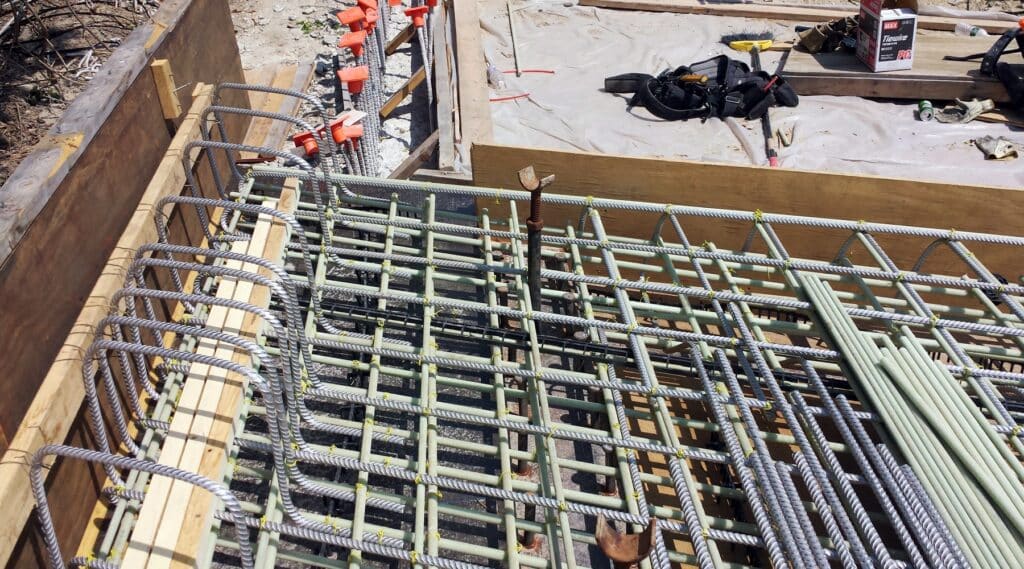
The available options to increase corrosion resistance in reinforced concrete and extending the life of our bridges are growing. There is no one solution when trying to balance costs and expected life of the structure, but with technology and advancing materials, our industry continues to work on ways to cut down on maintenance and extend the life and resiliency of our infrastructure.
Our bridge team is comprised of award-winning project managers and engineers who are experts at navigating clients through regulations, budgeting, safety inspections, design, and construction, and ongoing maintenance. Is there a bridge in your community that needs service, or would you like to learn more about other advancements in bridge design? Contact me!
*It’s Hoyle Tanner’s 50th anniversary this year! Keep an eye on our Facebook, LinkedIn, and Twitter feeds for articles and anniversary news!